 |
 |
 |
 |
 |
|
|
 |
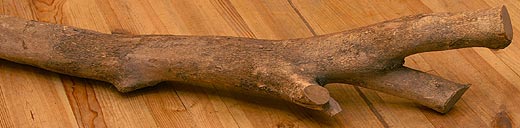
We mainly use maple, boxwood, rosewood, ebony, grenadilla and cherry. We are also experimenting with other types of woods now. Blocks are made of cedar wood. We use Florida cedar wood.
Additional materials are cork, silk thread, imitation ivory and grease.
In addition to these, there are attachments (such as keys).
|
Materials for the body and block |
|
Woods used for making recorders are best hard and dense for good tone quality, and easy to work on, clear of any knotty blemishes. On selecting woods, for example, I try striking two billets of the same material. If it sounded nice and clear, it would be one of the possible “good woods.”
|
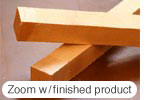 |
Maple is most widely used. Canadian and European maples are well- known, but I use “Mono maple (Itaya Kaede)” from Hokkaido, which is a hard specie of maple. This is one of the more tractable materials. As large pieces are available, it is used for large instruments such as tenor and bass recorders. Maple is also used for various musical instruments other than recorders, e.g. violin and harp. Recorders made of maple have soft and clear tone. |
 |
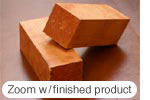 |
Cherry is also a domestic product, and relatively large pieces are available. It is quite hard, and hard on the blade. It smells very sweet while I work on it. The tone, too, is sweet and clear. It is a reliable material for making recorders. I use the wood chips for cooking – they make excellent smoking chips! |
 |
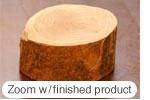 |
Boxwood is the material most favoured by players. It is my favourite, too. This is mostly a domestic product, too. European boxwoods from France or Britain are renowned. They are hard, easy to work on and wonderful, but unfortunately, recently they have become more difficult to come by worldwide. |
 |
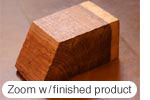 |
Rosewood comes from the South America. It is hard and heavy. It is often used for marimba, and sounds very loud. Rosewood recorders have a forceful and dominant tone. Once I made the clappers with rosewood to use on the night fire patrol for the neighbourhood association. |
 |
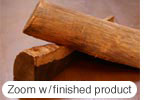 |
Ebony and Grenadilla originate in Africa. They are very heavy, with specific weight of 1.4. They are used for the fingerboards of string instruments and for clarinets. Their strong tone is popular with players, but they are difficult to handle as materials because they are hard and dense and thus prone to cracking during seasoning and manufacture. |
 |
 |
A type of Cedar wood is used for the block. It comes from Florida. Block material requires resistance to moisture and to deformation, as it gets wet regularly. The fresh wood has a distinct scent. Insects seem to dislike the scent, so we put some pieces in the wardrobe in place of moth repellent. |
|
|
 |